Selecting a Motor: Selection Points
Since each model has different characteristics, the points for selection (items to be confirmed) are also different.
AC Motors
① Rotation Speed Fluctuation by Load
The actual rotation speed of the AC motor is a few percent less than the synchronous speed due to the influence of load torque.
When selecting an AC motor, the selection should take this decrease in speed into account.
② Time Rating
There are differences in continuous rating and short time rating depending on the motor type, even if motors have the same output power. Motor selection should be based on the operating time (pattern).
③ Permissible Load Inertia of the Gearhead
If instantaneous stop (using a brake pack etc.), frequent intermittent operations, or instantaneous bi-directional operation will be performed using a motor with a gearhead, an excessive load inertia may damage the gearhead. The permissible load inertia of the gearhead has been specified. Therefore, the selection must be made so the load inertia does not exceed the permissible load inertia of gearhead.
Brushless Motors
① Permissible Torque
Motor combination types with a gearhead attached are listed on the permissible torque table based on the gearhead output shaft. Select products in which the load torque does not exceed the permissible torque.
② Permissible Inertia
A permissible inertia is specified for the brushless motor for avoiding alarms due to the regenerative power during deceleration and for stable speed control. Select products in which the inertia does not exceed the permissible value.
In the case of a product with a gearhead attached to the motor, if the inertia of the load becomes excessive, there is a possibility that the gearhead may be damaged. When attaching the gearhead, there is a specified permissible inertia. Select a product that does not exceed this value.
③ Effective Load Torque
When operating theBXII Series with frequent starts and stops, make sure the effective load torque does not exceed the rated torque. If it is exceeded, the overload protective function activates and stops the motor.
αSTEP/Stepper Motors
① Confirm the Required Torque
For αSTEP and stepper motors, select motors whose duty region (operating speed NM (f2) and the required torque TM) falls within the pullout torque curve.
Safety Factor Sf (Reference value)
Applicable Products | Safety Factor (Reference value) |
---|---|
αSTEP | 1.5~2 |
2-Phase and 5-Phase Stepper Motors | 2 |
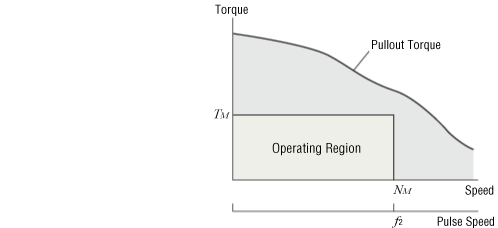
② Considerations for Temperature Rise
The αSTEP and stepper motor will increase the temperature rise if operated continuously over a long period of time. Exceeding the temperature of insulation class (Class B 130 °C) inside the motor may deteriorate its insulating performance. Temperature rise will vary based on the operating speed, load conditions and installation conditions. As a reference, the stepper motor should be used at an operating duty of 50 % or less. If the operating duty exceeds 50 %, choose a motor with a sufficient margin of torque or use methods to lower the operating current.
③ Confirm the Inertia Ratio
Calculate the inertia ratio using the following formula:
For Geared Motors
Large inertia ratios in αSTEP and stepper motors cause large overshooting and undershooting during starting and stopping, which can affect rise times and settling times. Furthermore, pulse signals may exhibit a step-like change in pulse speed during acceleration/deceleration, with the step size increasing with more abrupt changes in acceleration or deceleration. Therefore, if the inertia ratio is large, operation may not be possible. Check that the inertia ratios are less than or equal to the reference values shown in the table so that the selected motor can be operated more reliably.
Inertia Ratio (Reference values)
Applicable Products | Inertia Ratio |
---|---|
αSTEP | 30 max. |
2-Phase and 5-Phase Stepper Motors | 30 max. |
When the values in the table are exceeded, we recommend a geared type.
Servo Motors
① Permissible Load Inertia
A permissible load inertia is specified for the servo motor for stable control. The load inertia of the servo motor must not exceed the permissible value.
Applicable Products | Permissible Load Inertia |
---|---|
AZX Series NX Series |
Rotor inertia of 50 times max.* |
- *Automatic tuning allows operation up to 50 times the rotor inertia; manual tuning allows operation up to 100 times the rotor inertia (NX Series).
② Rated Torque
The motor can be driven when the ratio of load torque TL and rated torque of the servo motor is 1.5∼2 or more.
③ Maximum Instantaneous Torque
Confirm that the required torque is no higher than the maximum instantaneous torque of the servo motor. (Ensure that the safety factor of required torque Sf is at 1.5∼2 or more.) Note that the time that maximum instantaneous torque can be used for varies depending on the motor.
Maximum Instantaneous Torque and Operating Time
Applicable Products | Operating Time | Maximum Instantaneous Torque |
---|---|---|
AZX Series NX Series |
Within approx. 0.5 seconds | At 3 times the rated torque (at rated speed)* |
- *AZX series rated output 600W type is 3.75 times the rated torque.
④ Effective Load Torque
The motor can be driven when the effective load safety factor, which is the ratio of an effective load torque and a rated torque of servo motor, is 1.5∼2 or more.
⑤ Settling Time
There is a time lag between a position command sent and the servo motor's actual operation. This difference is called the settling time. Therefore, the actual positioning time is the sum of the positioning time calculated from the operating pattern and the settling time.
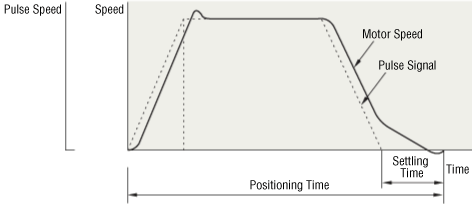
-
The settling time varies when the gain parameter is changed by the mechanical rigidity setting switch.