AC Motors Structure and Operation of Clutch and Brake Motors
The figure to the right shows the structure of the clutch and brake motor. In the absence of applying 24 VDC to both the clutch coil and brake coil, the output shaft can move freely.
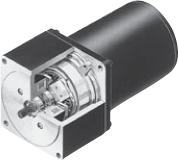
Operation
When 24 VDC is applied to the clutch coil, the armature of the clutch coil is drawn against the clutch plate, transmitting motor rotation to the output shaft.
The motor is constantly rotating.
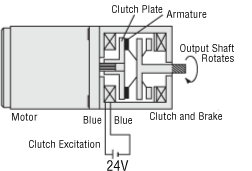
Stopping and Load Holding
By turning the clutch coil excitation off after a certain time lag, applying 24 VDC to the brake coil will cause the armature on the brake to come into contact with the brake disk, which will cause the output shaft to come to a stop. During braking, the output shaft is released from the motor, so the inertia from the motor has no effect. The motor is constantly rotating.
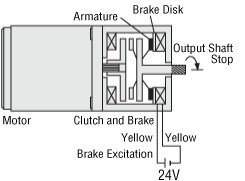
The following figure illustrates the movement of the motor shaft and output shaft, as well as the excitation state of the clutch and brake.
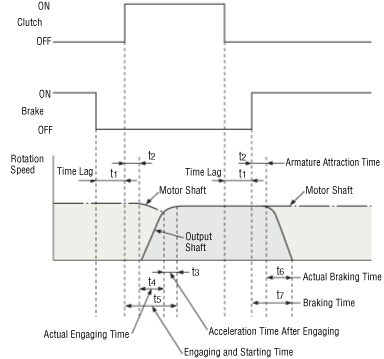
Operation
When operation is shifted from holding the load to moving the load, a time lag of 20 ms or more is required after releasing the brake and before applying voltage to the clutch. (This is to prevent the clutch and brake from engaging at the same time.)
The time required for the clutch and brake output shaft to reach a constant speed after applying voltage to the clutch is referred to as the engaging and starting time (t5) and is calculated by adding up the following time elements.
- ①
- Armature Attraction Time t2
The time required for the armature to come into contact with the clutch after voltage application to the clutch.
- ②
- Actual Engaging Time t4
The time required for the clutch/brake output shaft, which is accelerated by dynamic friction torque, to engage completely with the motor shaft after the armature comes in contact with the clutch.
- ③
- Acceleration Time after Engaging t3
The time needed to accelerate to the required speed when load is suddenly applied to the motor during the actual engaging time described in ②, causing a temporary drop in speed.
Braking
When the operating status is shifted from rotation to stopping or holding a load, a time lag of 20 ms or more is required after releasing the clutch and before applying voltage to the brake. The time required for the clutch and brake output shaft to come to a stop after applying voltage to the brake is referred to as the braking time (t7) and is calculated by adding up the following time elements.
- ①
- Armature Attraction Time t2
The time required for the armature to contact with the brake disk after voltage application to the brake.
- ②
- Actual Braking Time t6
The time required for rotation of the clutch/brake output shaft to come to a stop after the armature comes into contact with the brake disk.
Linked Starting Characteristics (Reference values)
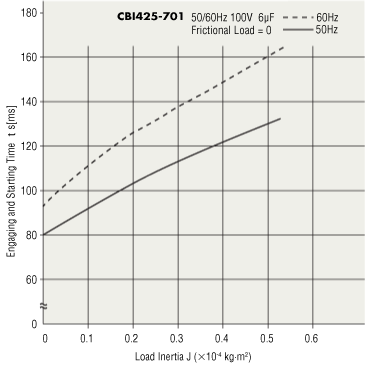
Braking Characteristics (Reference values)
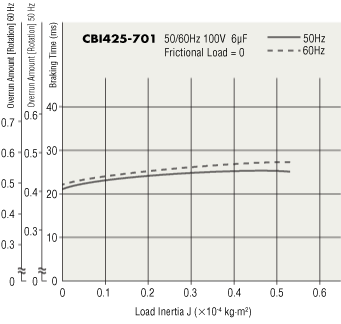