αSTEP/Stepper Motor: Operating Principles of the Stepper Motor
When magnetized, the actual positional relationship of the teeth between the stator and rotor in a 5-phase stepper motor is explained as a practical example.
When Phase A is Excited
When exciting Phase A, the magnetic pole is magnetized as the South pole. Rotor 1, with teeth having the North pole polarity, is attracted, while Rotor 2, with teeth having the South pole polarity, is repelled. They balance each other, resulting in a stop. At this time, the teeth of the magnetic pole in Phase B, which is not excited, are offset by 0.72° from the teeth of Rotor 2, which has the South pole polarity. This describes the positional relationship between the teeth of the stator and rotor when exciting Phase A.
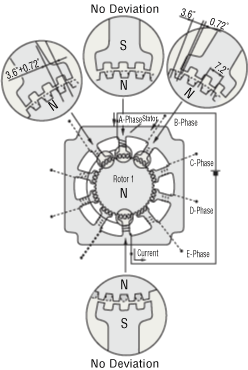
When Phase B is Excited
Next, when switching from exciting Phase A to exciting Phase B, the magnetic pole of Phase B is magnetized as the North pole. It attracts Rotor 2, which has the South pole polarity, and repels Rotor 1, which has the North pole polarity.
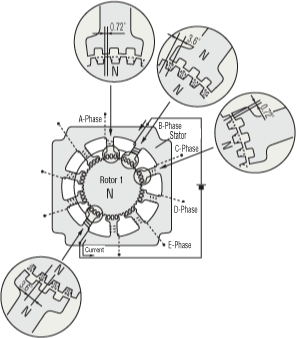
In other words, by switching the excited phase from Phase A excitation to Phase B excitation, the rotor has rotated by 0.72°. As evident from this, by sequentially switching the excitation phase from Phase A to Phase B, Phase C, Phase D, Phase E, and back to Phase A, the stepper motor rotates precisely by 0.72° each time. Similarly, if you want to rotate in the opposite direction, you can achieve this by reversing the order of excitation from Phase A to Phase E, Phase D, Phase C, Phase B, and back to Phase A.
The high resolution of 0.72° is generated by mechanical tolerances in the structure of the stator and rotor. This is the reason why accurate positioning can be achieved without the need for sensors such as encoders. In addition, a high stopping accuracy of as much as ±3 minutes (with no load) can be achieved because there is only variation in the finishing accuracy and assembly precision of the stator and rotor, and the DC resistance of the windings. In actual stepper motors, the driver is responsible for switching the excitation phase, and the timing of this switching is controlled by pulse signals input to the driver. While the example provided demonstrates exciting one phase at a time, in practice, to effectively utilize windings, 4-phase or 5-phase simultaneous excitation is commonly employed.