αSTEP/Stepper Motor: Driver Section of the Stepper Motor
There are 2 types of stepper motor drive systems: constant current drive system and constant voltage drive system.
The constant voltage drive system has a simple circuit configuration, but it is difficult to obtain favorable torque characteristics at high speeds.
On the other hand, the constant current drive system is a widely used drive system today and has excellent torque characteristics at high speed area. All of Oriental Motor’s stepper motor drivers use this drive system.
Overview of Constant Current Drive System
Stepper motors rotate by sequentially switching the current flowing through each winding. However, as the rotation speed increases, the switching becomes faster, and the current rise cannot keep up, resulting in a decrease in torque.
Therefore, by chopping the direct current voltage at a much higher level than the motor's rated voltage, it is possible to maintain the rated current in the motor even at high speeds.
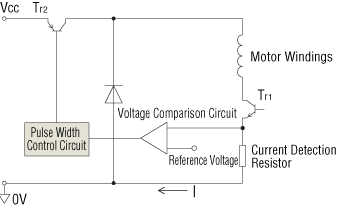
The current flowing through the motor winding is extracted as voltage using a current sensing resistor and compared with a reference voltage. When the voltage of the sensing resistor is lower than the reference voltage (when the rated current is not reached), the switching transistor Tr2 is continuously turned on, and when the voltage is higher than the reference voltage (when the rated current is exceeded), Tr2 is turned off, and the current is controlled so that the rated current always flows.
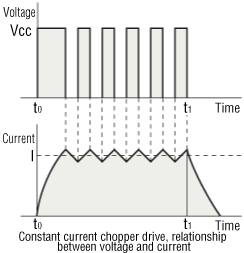
Difference in Characteristics Between AC Input and DC Input
The stepper motor is driven by applying DC voltage through a driver.
For Oriental Motor's products, 24 VDC is applied to the motor in the case of 24 VDC input products, and approximately 140 VDC is applied to the motor after rectification to DC in the case of 100 VAC and 200 VAC input products. (Except for some products.)
The difference in applied voltage to this motor results in variations in torque characteristics, especially in the high-speed range. That is because the rise of the current flowing through the motor windings becomes faster with higher applied voltage, allowing the rated current to flow even in the high-speed range. In other words, AC input products excel in torque characteristics across a wide range, from low-speed to high-speed, allowing for significant speed ratios.
Oriental Motor recommends first using an AC input product that can handle the various operating conditions of the device.
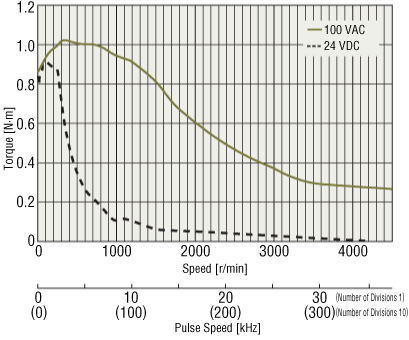
Microstep Technology
The basic step angle of a 5-phase stepper motor, 0.72°, can be further subdivided without a mechanical reduction mechanism, achieving finer divisions (up to a maximum of 250).
Features
Since stepper motors rotate and stop at each step angle determined by the salient-pole structure of the rotor and stator, position control is highly accurate and easy. However, conversely, the rotor undergoes speed changes with each step angle rotation, exhibiting characteristics such as resonance at certain rotation speeds and increased vibration.
Microstep drive is a technology that subdivides the basic step angle of the motor by controlling the current flowing through the motor coils, enabling ultra-low-speed and low-noise operation.
- The basic step angle of the motor (0.72˚/full step) can be subdivided into 1/1 to 1/250, enabling smooth operation with micro angle feed.
- The technology to smoothly vary the motor's driving current has enabled the suppression of motor vibrations, achieving low-noise operation.
Characteristics
-
Low Vibration
Microstep technology electrically subdivides the step angle. It has significantly improved vibrations by smoothing out incremental movements in the low-speed range.
Normally, dampers are used to reduce vibrations, but by adopting low-vibration design for the motor itself and incorporating microstep technology, further reduction in vibrations is achieved.
It is ideal for applications or devices sensitive to vibrations, as significant simplification of vibration countermeasures can be achieved. - Noise Reduction
Microstep technology has improved vibration noise in the low-speed range, achieving reduced noise levels.
It performs effectively even in environments where noise reduction is crucial. -
Improvement in Controllability
It is a microstep drive using a new pentagon method with excellent damping characteristics.
There is minimal overshoot and undershoot for each step, and it accurately follows the pulse pattern. (This also improves linearity.)
It can also soften the shock of starting and stopping.
How to Choose a Power Transformer
When stepper motors are used overseas, most places use a single-phase 115 VAC or single-phase 220-240 VAC power supply. If you are using it in those regions, please use it in accordance with the power supply input specifications through a power transformer.
The transformer capacity can be determined using the following formula.
Transformer Capacity [VA] = Driver Power Supply Voltage [V] × Driver Input Current [A]
The driver input current for a stepper motor can be obtained from the specifications list and the speed-torque characteristics.
Refer to here for information on using standard certified products overseas.