αSTEP/Stepper Motor: Stepper Motor Basic Characteristics
When using a stepper motor, it is important to ensure that the motor’s characteristics are suitable for the operating conditions.
Here, we will explain the characteristics that are important when using a stepper motor.
The characteristics of stepper motors can be broadly classified into 2 categories.
- Dynamic Characteristics:
The characteristics related to the starting or rotation of a stepper motor primarily affect the operation and cycle time of the equipment. - Static Characteristics:
The characteristics related to the angle change when a stepper motor is stopped primarily affect the accuracy of the equipment.
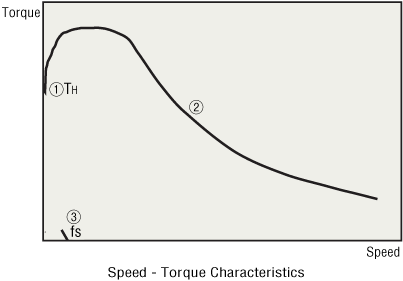
Dynamic Characteristics
Speed - Torque Characteristics
The characteristics diagram shows the relationship between the rotation speed and torque when driving a stepper motor.
This is a characteristic that is essential to use when selecting a stepper motor. The horizontal axis represents the rotation speed of the motor output shaft, and the vertical axis represents the torque.
The speed - torque characteristics are determined by the motor and driver, so they are greatly affected by the type of driver being used.
- ①
- ① Maximum Holding Torque (TH: Holding Torque)
This refers to the maximum holding torque (holding force) that a stepper motor has when it is in a powered-on state (rated current) and at a standstill.
- ②
- ② Pullout Torque
It is the maximum instantaneous torque that can be produced at each rotation speed.
When selecting a motor, be sure that the required torque falls within this curve.
- ③
- Maximum Starting Frequency (fS)
This is the maximum pulse speed at which the motor can start and stop instantaneously (without an acceleration/deceleration time) when the frictional load and load inertia of the stepper motor are 0.
Driving the motor at a pulse speed of this rate or more will require a gradual acceleration/deceleration. This frequency drops when there is a load inertia on the motor.
(Refer to the load inertia - starting frequency characteristics)
Maximum Response Frequency (fr)
This is the maximum pulse speed at which a stepper motor can operate by gradual acceleration/deceleration when the frictional load and load inertia are 0.
The figure below shows the speed - torque characteristics of a typical 5-phase stepper motor.
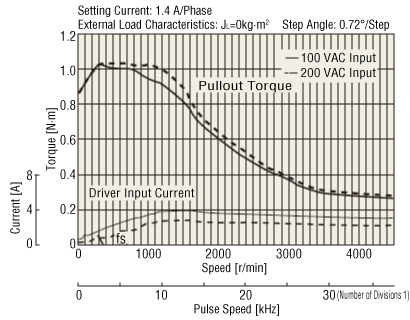
Load Inertia - Starting Frequency Characteristics
These characteristics show the variation in starting frequency due to load inertia.
The stepper motor’s rotor itself and the load have inertia, which causes delays and advances in the motor shaft during instantaneous starting and stopping. This value varies depending on the pulse speed, but if it exceeds a certain value, the motor will not be able to follow the pulse speed and will go out of step (misstep).
The pulse speed just before the system goes out of step is called the starting frequency.

The variation of the maximum starting frequency with respect to the load inertia can be approximated by the following formula.
- fS
- Maximum starting frequency of motor alone [Hz]
- f
- Maximum starting frequency with load inertia [Hz]
- JO
- Rotor inertia [kg·m2]
- JL
- Load inertia [kg·m2]
Vibration Characteristics
The stepper motor rotates in a continuous step-like motion. The response of one step, observed in the form of step-like motions, is referred to as the single-step response below.
- ①
- When a single pulse is input to a stopped stepper motor, it accelerates toward the next step angle.
- ②
- The accelerated motor passes through the step angle, overshoots a certain angle, and then is pulled back in the opposite direction.
- ③
- After undergoing such damped oscillation, it comes to a stop at the designated step angle position.
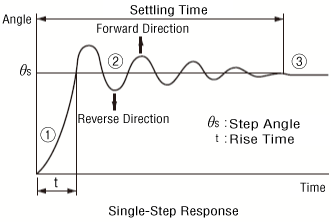
The step-like motion that produces this damped oscillation is the cause of the vibration at low speeds.
The vibration characteristics are the characteristics that show the magnitude of vibration while the stepper motor is rotating.
The lower the vibration level, the smoother the rotation.
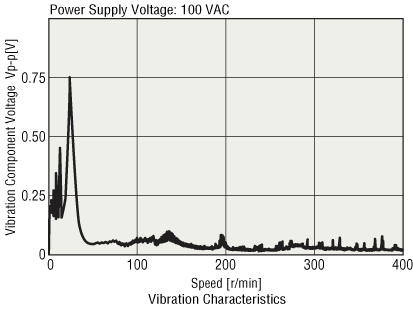
Static Characteristics
Angle - Torque Characteristics
When a motor is excited at the rated current and torque is externally applied to the motor shaft to change the angle of the rotor, the relationship between the angle and torque is called angle - torque characteristics, as shown in the figure below.
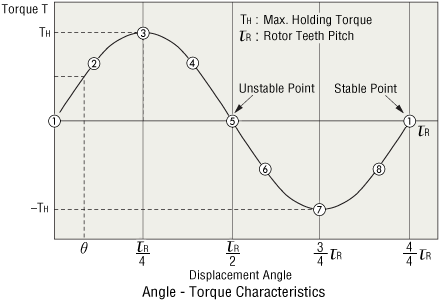
The following figure shows the positional relationship of the small teeth between the stator and rotor at each point in the characteristics diagram above.
If an external force is applied to the motor shaft when it is equilibrated and stopped at the stable point ①, torque T (+) is generated in the left side to pull it back to the stable point ①, and it stops at an angle equilibrated with the external force. ②
There is an angle at which the maximum generated torque is reached when further external force is applied. The generated torque at that time is the maximum holding torque TH. ③ If an external force is applied that exceeds this point, a torque T (-) will be generated in the same direction as the external force through the unstable point ⑤, and it will move to the next stable point ① and stop.
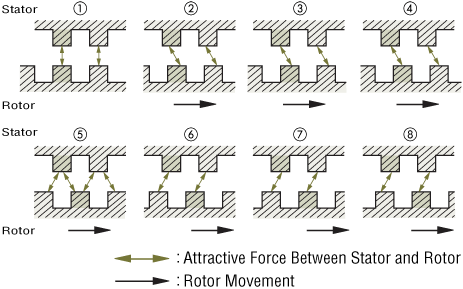
Stable Point:
This is the place where the small teeth on the stator and rotor stop in a perfectly relative position. It is very stable and always stops at this location when the external force is set to 0.
Unstable Point:
This is the place where the small teeth of the stator and rotor are offset by 1/2 pitch. It is very unstable and will move to the right or left stable point if any external force is applied.
Angular Accuracy
The stepper motor has an angular accuracy of within ±3 arcmin (0.05˚) with no load condition. The small error is due to the mechanical accuracy of the stator and rotor, and the small resistance variation of the stator winding.
The following stop position accuracy is commonly used to express the angular accuracy of stepper motors.
Stop Position Accuracy:
This refers to the discrepancy between the theoretical and actual stop positions of the rotor. It represents the difference between the maximum (+) value and the maximum (-) value when measuring 360˚ step by step from any arbitrary stop position of the rotor.
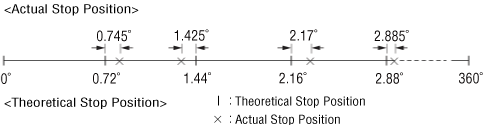
The stop position accuracy is within ±3 arcmin, but only under no-load conditions.
However, in actual applications, there is always a frictional load.
In such cases, the angular accuracy is influenced by the angle - torque characteristics, which results in angle variation according to the frictional load. If the frictional load is constant, the displacement angle will be constant for unidirectional operation. However, in bi-directional operation, double the displacement is produced over a round trip.
When high stopping accuracy is required, always position from one direction only.
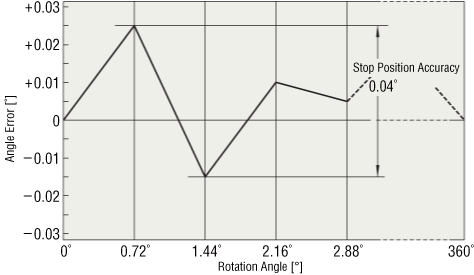