Servo Motor: Control Block Diagram of Servo Motors
It counts the pulse signal given from the outside (in the case of pulse input type) and the rotation detected by the encoder of the servo motor, and outputs the difference (deviation) to the speed control section. We call this counter the deviation counter.
During motor rotation, accumulated pulses (= position deviation) are generated in the deviation counter, which is controlled to set the accumulated pulses to 0.
A position loop (deviation counter) is a function used to hold the present position (position holding by servo lock).
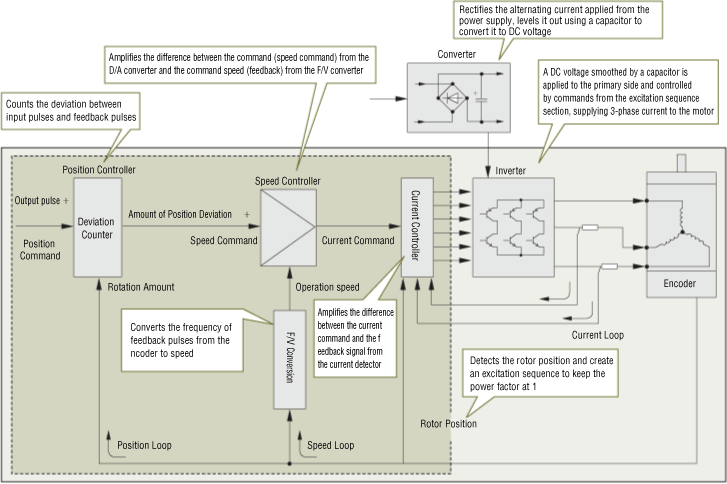
A servo motor consists of 3 elements: a motor, encoder, and driver. The driver is responsible for controlling the drive current by comparing the position command with the position and speed information from the encoder. A servo motor constantly detects the state of the motor from the position and speed information of the encoder. Therefore, even if the motor stops, the servo motor can output an alarm signal to the controller, allowing the detection of abnormal conditions. Servo motors need to adjust control system parameters according to the rigidity of the mechanism and load conditions. However, in recent years, real-time automatic tuning has made this adjustment easier.